Accumulation Tables
Garvey Accumulation Solutions
Are bottlenecks and product damage holding back your production efficiency?
Discover how Garvey’s suite of accumulation tables can revolutionize your line performance.
Imagine a production line that never stops, where products flow seamlessly without damage or delay. From delicate vials to wine bottles, Garvey has a solution designed for your specific needs.
Why Choose Garvey Accumulation Tables?
- Unmatched Speed & Precision: Handle products at rates up to 800 units per minute
- Versatility: Solutions for every industry, from pharmaceuticals to beverage
- Space Efficiency: Compact designs with vertical accumulation options
- Low Maintenance: Simple, reliable designs minimize operational costs
- Industry-Proven: Trusted by leading manufacturers worldwide
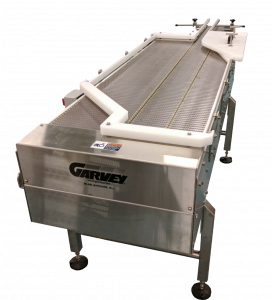
Bi-Flo™ Accumulation Tables
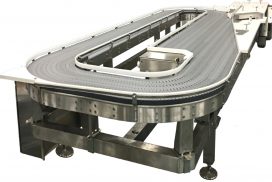
Infinity™ Accumulation Tables
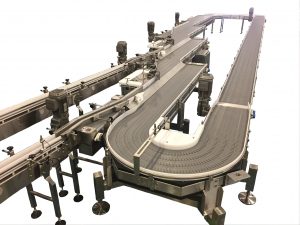
3D Infinity™ Accumulator
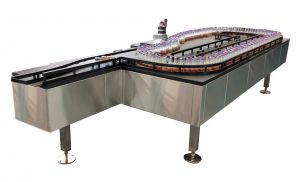
Infinity™ RX Series
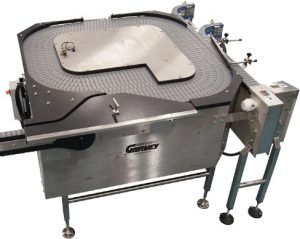
Infinity™ RX Rotary Replacement Models
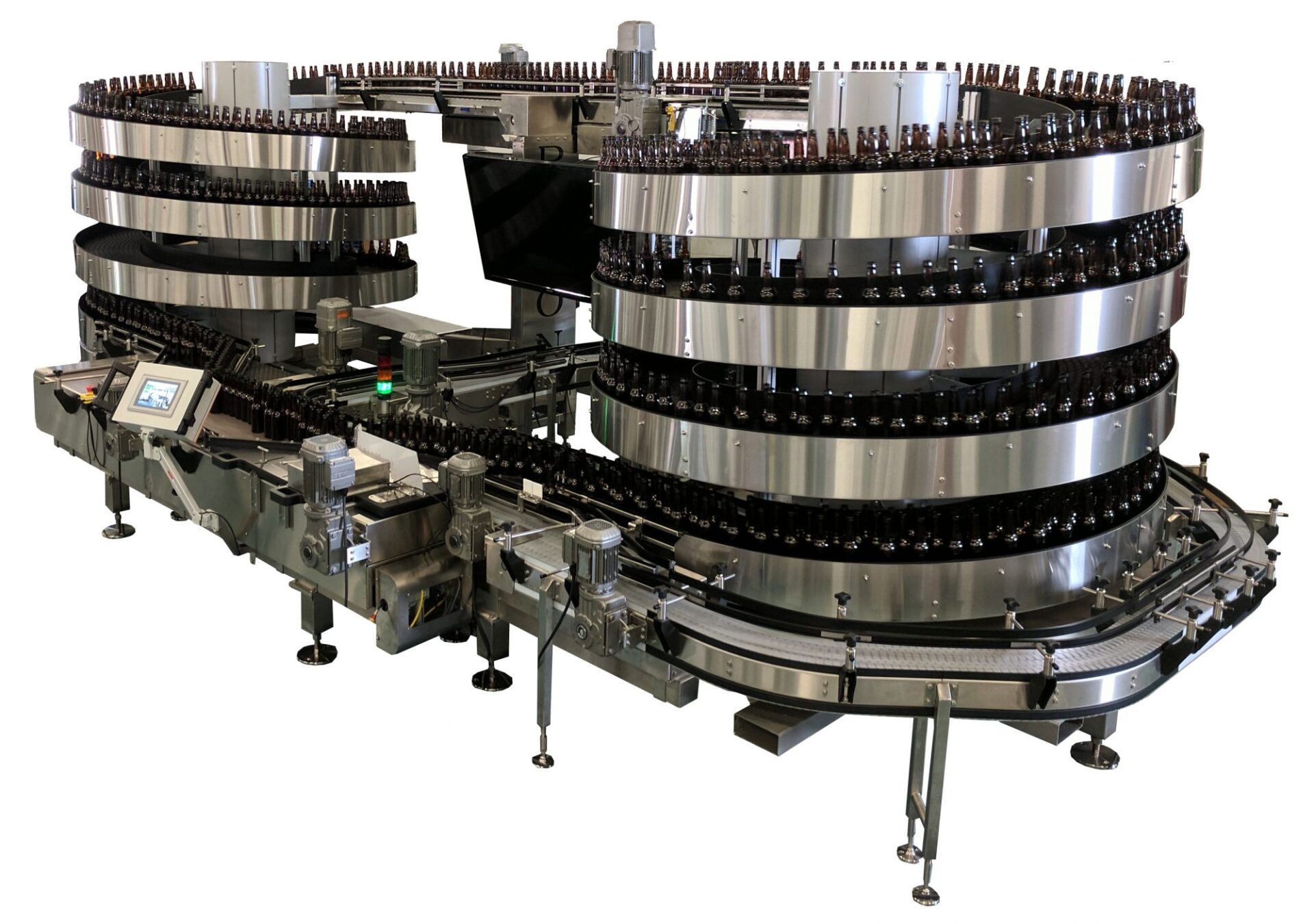
Spiral Infinity™ Accumulation Tables
Combining Garvey’s Infinity technology with Ryson’s spiral system, the Spiral Infinity™ tables offer vertical accumulation for maximum space efficiency. Capable of handling full or empty bottles, cans, jars, and other containers, these tables convey products up and down in single file or continuous mass flow. They’re the ideal solution for facilities with limited floor space, maximizing vertical space utilization without compromising on performance.
Garvey’s Guide To Accumulation Tables
Definition Of Accumulation Tables
An accumulation table is a specialized type of conveyor system designed to temporarily hold and accumulate products or materials. These tables can be circular (also known as rotary accumulation tables), rectangular, or even custom-shaped to fit specific production line requirements. They serve as a buffer zone in the production process, allowing for the smooth flow of items between different stages of manufacturing or packaging.
Importance In Industrial Settings
Accumulation tables are vital in maintaining efficiency and continuity in production lines. They offer several key benefits:
- Buffer capacity: By providing a space for products to accumulate, these tables prevent slowdowns and ensure a steady flow of items, even when there are variations in production speed or temporary stoppages in different parts of the line.
- Product protection: Accumulation tables, especially those utilizing zero-pressure or minimum-pressure accumulation methods, reduce the risk of product damage by minimizing contact between items.
- Production line balancing: These tables help balance production lines by accommodating differences in processing times between various stages of manufacturing.
- Improved worker safety: By automating the accumulation process, these tables reduce the need for manual handling, thereby enhancing workplace safety.
- Space optimization: Rotary accumulation tables, in particular, offer an efficient way to accumulate products in a compact footprint, making them ideal for facilities with limited floor space.
Brief History And Evolution
The concept of accumulation in conveyor systems has been around for decades, evolving alongside the growth of mass production and automation. Early accumulation tables were simple rotating platforms, often manually operated. As manufacturing processes became more complex and automated, so did accumulation tables.
Modern accumulation tables incorporate advanced features such as:
- Sensor-based accumulation control
- Variable speed drives for enhanced efficiency
- Integration with Industry 4.0 and IoT technologies
- Customizable designs to accommodate various product types and sizes
- Energy-efficient motors and components
From basic rotary tables to sophisticated bi-directional accumulation tables and even packaging-specific accumulation tables, the technology continues to advance to meet the ever-changing needs of industry.
As we delve deeper into the world of accumulation table solutions, we’ll explore their working principles, types, applications, and the latest innovations shaping their future in industrial material handling.
How Accumulation Tables Work
Accumulation table conveyors are sophisticated systems designed to efficiently manage the flow of products in industrial settings. Understanding their operation is crucial for manufacturers, engineers, and operators looking to optimize their production lines.
Basic Operating Principle
The fundamental principle of accumulation tables is to provide a controlled area where products can accumulate and be released as needed. This process involves:
- Inflow: Products enter the accumulation table from a feed conveyor.
- Accumulation: Items are held on the table, often in a circular or spiral pattern.
- Outflow: Products are released onto an exit conveyor as downstream processes become available.
Key Components
Conveyor Belts or Rollers
Accumulation tables use either belts or rollers to move products. Belt-driven systems are ideal for smaller, lighter items, while roller systems can handle heavier loads. Some advanced designs incorporate stainless steel components for food-grade applications or harsh environments.
Drive Systems
Electric motors power the movement of the conveyor. Many modern systems use variable speed drives to adjust the accumulation rate and optimize energy efficiency.
Control Mechanisms
Sophisticated control systems, often PLC-based, manage the flow of products. These may include:
- Sensors to detect product presence and position
- Logic controllers to manage accumulation and release
- User interfaces for operator control and monitoring
Types of Accumulation Methods
Zero-Pressure Accumulation
- Individually controlled zones on the conveyor
- Sensors that detect product presence in each zone
- Logic that stops each zone when a product is present and the next zone is occupied
Zero-pressure accumulation is ideal for delicate products or industries where product damage must be minimized, such as electronics or beverage bottling.
Minimum-Pressure Accumulation
This method allows products to make contact with each other, but with minimal force. It’s achieved through:
- Slip clutches or torque-limiting devices on rollers
- Variable speed controls that slow the conveyor as it fills
- Specialized belt materials that allow controlled slippage
Minimum-pressure accumulation is often used in packaging applications where some contact between products is acceptable.
Design Considerations
When designing an accumulation table conveyor, several factors must be considered:
- Product Characteristics: Size, weight, and fragility of items determine the type of conveyor and accumulation method.
- Throughput Requirements: The system must be able to handle the required volume of products per hour.
- Space Constraints: Round or spiral designs can optimize floor space in facilities with limited area.
- Integration: The system must seamlessly connect with existing conveyor lines and machinery.
- Environmental Factors: Considerations like temperature, humidity, and cleanliness requirements (especially in food-grade applications) influence material choices and design.
Advanced Features
- Bi-directional Capability: Some tables can accumulate and dispense products in either direction, providing greater flexibility.
- Modular Design: This allows for easy expansion or reconfiguration of the system.
- Data Collection and Analysis: Integration with manufacturing execution systems (MES) for real-time performance monitoring and optimization.
- Predictive Maintenance: Sensors and AI algorithms can predict when maintenance is needed, reducing downtime.
Understanding these principles and components is essential for selecting, operating, and maintaining an efficient accumulation table conveyor system. As technology advances, these systems continue to evolve, offering increasingly sophisticated solutions for material handling challenges.
Accumulation Tables & Accumulation Conveyors: Understanding the Difference
Accumulation Tables
Accumulation tables are typically stationary or rotating platforms designed to temporarily hold and organize products. Key features include:
- Design: Usually circular or rectangular platforms, often with a rotating surface.
- Movement: Products may rotate on the table but don’t travel long distances.
- Capacity: Limited by the table’s surface area.
- Application: Ideal for temporary storage, product orientation, or as buffers between processes.
- Examples: Rotary accumulation tables, lazy susan-style tables.
Accumulation Conveyors
- Design: Linear or curved conveyor belts or roller systems, often with multiple zones.
- Movement: Products travel along the conveyor while accumulating.
- Capacity: Can handle larger volumes over longer distances.
- Application: Suitable for managing product flow between different production stages, especially in high-volume operations.
- Examples: Belt conveyors with accumulation zones, roller conveyors with zero-pressure accumulation.
Key Differences
- Mobility: Accumulation tables generally keep products in a confined area, while accumulation conveyors transport products over distances.
- Flow Management: Tables are better for batch processing or reorienting products, while conveyors excel at continuous flow management.
- Space Utilization: Conveyors can maximize linear space usage, while tables are more compact and can utilize vertical space (in the case of multi-level tables).
- Flexibility: Accumulation conveyors often offer more flexibility in terms of product routing and line balancing.
- Integration: Conveyors are typically easier to integrate into a continuous production line, while tables are often used as standalone buffer stations.
Choosing the Right Solution
The choice between an accumulation table and an accumulation conveyor depends on several factors:
- Production volume and speed
- Available floor space
- Nature of the products being handled
- Specific process requirements (e.g., need for product reorientation)
- Integration with existing systems
In many advanced production lines, a combination of both accumulation tables and conveyors may be used to optimize product flow and maximize efficiency.
Understanding these differences is crucial for selecting the right accumulation solution for your specific production needs. Garvey offers a range of both accumulation tables and accumulation conveyors, each designed to meet unique industrial requirements. For expert guidance on choosing the best accumulation solution for your operation, contact Garvey or visit our Products page to explore our innovative offerings.
Types of Accumulation Solutions
Belt-driven Accumulation Conveyors
Belt-driven systems are versatile and widely used in many industries.
- Straight Belt Accumulators:
- Ideal for long, straight production lines
- Often used in bottling and canning operations
- Can handle empty or filled bottles efficiently
-
Serpentine Belt Accumulators:
- Maximize accumulation capacity in a smaller footprint
- Commonly used in brewery and beverage packaging
Manufacturers like Garvey offer advanced belt-driven systems with features such as low-pressure accumulation for gentle handling of products.
Roller Accumulation Conveyors
- Powered Roller Conveyors:
- Can handle boxes, crates, and other large items
- Often used in distribution centers and manufacturing plants
- Some models feature a lazy Susan design for easy access
- Gravity Roller Conveyors:
- Use gravity and slight inclines for product movement
- Energy-efficient option for suitable applications
- Often used in conjunction with powered systems
Companies like Garvey produce roller accumulation systems with various customization options, fitted for your business and your needs.
Spiral Accumulation Conveyors
- Vertical Spiral Accumulators:
- Utilize vertical space for maximum efficiency
- Can handle bottles, cans, and other cylindrical items
- Often used in beverage and personal care product lines
- Bi-Directional Spiral Accumulators:
- Allow for both accumulation and de-accumulation in the same unit
- Provide flexibility in production line layout
Companies like Garvey are known for our innovative spiral accumulator designs, such as the Infinity Series.
Rotary Accumulation Tables
- Single-Level Rotary Tables:
- Circular design for compact accumulation
- Often used as unscrambling tables in packaging lines
- Can handle bottles, vials, and small containers
- Multi-Level Rotary Accumulators:
- Maximize vertical space utilization
- Ideal for high-volume production environments, quickly removing the finished product
- Can significantly increase accumulation capacity
Pallet Accumulation Systems
These systems handle larger, palletized loads.
- Chain-Driven Pallet Accumulators:
- Robust systems for heavy-duty applications
- Often used in manufacturing and distribution centers
- Can handle wooden pallets, metal containers, and large boxes
- Roller Pallet Accumulators:
- Provide smooth movement for palletized goods
- Can be integrated with automated guided vehicles (AGVs) or forklifts
Specialized Accumulation Systems
- Sanitary Accumulation Tables:
- Made with stainless steel and designed for easy cleaning
- Used in food, beverage, and pharmaceutical industries
- Can handle wet environments and frequent washdowns
- High-Speed Accumulation Systems:
- Designed for industries with rapid production rates
- Often incorporate advanced sensors and control systems
- Used in bottling, canning, and packaging industries
-
Refrigerated Accumulation Tables:
- Maintain cold chain for temperature-sensitive products
- Used in food processing and pharmaceutical industries
Here at Garvey, we offer specialized accumulation systems for specific industry needs.
When selecting an accumulation table conveyor, consider factors such as:
- Product characteristics (size, weight, fragility)
- Production rate and accumulation capacity needs
- Available floor space and layout constraints
- Industry-specific requirements (e.g., sanitary design for food processing)
- Integration with existing equipment and systems
By understanding these various types and their applications, manufacturers can choose the most suitable accumulation table conveyor to optimize their production lines and improve overall efficiency.
Applications and Industries
Food Processing and Packaging
- Buffering products between processing and packaging stages
- Managing flow of items like baked goods, frozen foods, and ready meals
- Accumulating products for quality inspection and sorting
- Integrating with filling and sealing equipment in high-speed production lines
Beverage Industry
- Accumulation of bottles, cans, and containers in high-speed bottling lines
- Buffering products between filling and labeling operations
- Managing product flow in brewery operations and soft drink packaging
- Providing a buffer for pasteurization and cooling processes
Household & Personal Care
- Accumulation of containers before filling operations for cleaning products
- Buffer storage between filling and capping processes for personal care items
- Management of different product sizes and shapes in production lines
- Integrating with labeling and packaging equipment for cosmetics and toiletries
Contract Packaging
- Flexible accumulation solutions for various product types and sizes
- Buffer storage for batch processing of different client products
- Integration with sorting systems for efficient order fulfillment
- Managing product flow between custom packaging operations
Industrial Manufacturing
- Accumulation of parts and components before assembly
- Buffering of finished products before packaging or shipping
- Managing different production line speeds for just-in-time manufacturing
- Integrating with robotic systems and automated guided vehicles (AGVs)
Pet Health
- Accumulation of pet food containers and packaging
- Buffer storage between filling and sealing operations for pet medications
- Managing flow of pet care products in diverse shapes and sizes
- Integrating with quality control systems for pet health supplements
Pharmaceutical & Nutraceutical
- Accumulation of vials, bottles, and blister packs in controlled environments
- Buffer storage for quality control and inspection processes of medications
- Management of sterile products between filling and packaging stages
- Integrating with cleanroom environments for maintaining product purity
- Handling delicate nutraceutical products like softgels and capsules
In each of these industries, accumulation tables play a vital role in process optimization and efficiency improvement. Key benefits across sectors include:
- Enhanced Production Flow: Smoothing out speed differences between production stages
- Increased Efficiency: Reducing downtime and maximizing equipment utilization
- Product Protection: Gentle handling to minimize damage to sensitive items
- Flexibility: Adapting to various product sizes and shapes within the same line
- Quality Control: Providing buffer zones for inspection and sorting processes
- Space Optimization: Efficient use of production floor space with compact designs
Garvey’s expertise spans across multiple industries, from food and beverage to pharmaceuticals and beyond. Our motto, ‘We can handle it,’ isn’t just a slogan—it’s a promise backed by decades of innovation and customer satisfaction.
Explore our industry pages to see how Garvey’s accumulation solutions have transformed production lines across various sectors, or reach out to our team to discuss your specific needs.
Benefits of Accumulation Tables
Increased Efficiency and Productivity
- Smooth Production Flow
- Act as buffers between different production stages, reducing bottlenecks
- Allow for continuous operation even when parts of the line are temporarily stopped
- Enable efficient handling of products with varying processing times
- Optimized Line Balancing:
- Help balance production lines by accumulating products between faster and slower processes
- Reduce idle time for both machinery and workers
- Allow for more flexible production scheduling
- Enhanced Throughput:
- Increase overall production capacity by maintaining a constant flow of products
- Enable high-speed operations in bottling and packaging lines
- Facilitate quick changeovers between different product runs
Reduced Product Damage
- Gentle Handling:
- Minimize product-to-product contact, especially in zero-pressure accumulation systems
- Reduce breakage and damage in fragile items like bottles and vials
- Protect surface finishes of products during accumulation and transport
- Controlled Product Movement:
- Prevent crushing or deformation of packages in accumulation zones
- Maintain product orientation, crucial for subsequent processes like labeling or filling
- Reduce the risk of contamination in sensitive environments like pharmaceutical production
Improved Worker Safety
- Reduced Manual Handling:
- Decrease the need for workers to manually move or stack products
- Lower the risk of repetitive strain injuries and accidents
- Allow workers to focus on higher-value tasks instead of product movement
- Organized Workspace:
- Minimize clutter on the factory floor by efficiently managing product flow
- Reduce trip hazards and improve overall workplace safety
- Create clearer pathways for workers and equipment movement
Space Optimization
- Compact Footprint:
- Utilize vertical space with spiral or multi-level accumulation systems
- Maximize use of available floor space, especially with rotary accumulation tables
- Reduce the need for large buffer storage areas between processes
- Flexible Layout Options:
- Allow for creative production line layouts to fit existing facility constraints
- Enable easy reconfiguration of production areas as needs change
- Facilitate modular production line design for scalability
Enhanced Inventory Management
- Real-time Product Tracking:
- Integrate with inventory management systems for accurate stock levels
- Enable just-in-time production by precisely controlling product flow
- Facilitate batch tracking and quality control processes
- Improved Order Fulfillment:
- Allow for efficient accumulation of products for order assembly
- Enable faster response to customer orders by having readily available stock
- Reduce errors in order picking and packing processes
Cost Savings
- Reduced Labor Costs:
- Minimize the need for manual product handling and movement
- Lower labor requirements for product sorting and organizing
- Decrease overtime costs by improving overall production efficiency
- Energy Efficiency:
- Optimize energy usage by maintaining continuous production flow
- Reduce start-stop cycles in production equipment, lowering power consumption
- Enable the use of energy-efficient motors and controls in modern accumulation systems
- Maintenance and Longevity:
- Lower maintenance costs through reduced wear and tear on production equipment
- Extend the lifespan of packaging and processing machinery by regulating product flow
- Minimize downtime for repairs and maintenance with robust accumulation systems
Quality Control and Consistency
- Improved Inspection Opportunities:
- Provide buffer zones for in-line quality control checks
- Allow for systematic sampling and testing without disrupting production flow
- Facilitate easy removal of defective products from the production line
- Consistent Product Handling:
- Ensure uniform treatment of products during accumulation and transport
- Maintain product integrity through controlled environmental conditions
- Enable precise timing for processes like cooling, drying, or setting
Adaptability and Scalability
- Flexible Production Capacity:
- Easily adjust to varying production volumes and speeds
- Accommodate different product sizes and shapes with minimal changeover time
- Scale operations up or down based on demand without major line modifications
- Integration with Industry 4.0:
- Incorporate smart sensors and data analytics for predictive maintenance
- Enable real-time production monitoring and adjustment
- Facilitate integration with broader manufacturing execution systems (MES)
By leveraging these benefits, companies can significantly improve their operational efficiency, product quality, and bottom line. Accumulation tables prove to be a valuable investment for businesses looking to optimize their production processes and stay competitive in today’s fast-paced manufacturing environment.
Design Considerations
Load Capacity and Dimensions
- Product Specifications:
- Calculate the total sum of products to be accumulated
- Consider the size, shape, and weight of items (e.g., bottles, eggs, plastic parts)
- Factor in variations in product dimensions for flexible designs
- Table Dimensions
- Determine the appropriate diameter for rotative or tournante (rotating) tables
- Consider square or rectangular designs for specific applications
- Ensure the design accommodates the maximum load without compromising performance
Speed and Throughput Requirements
- Production Line Integration:
- Match the accumulator speed with upstream and downstream processes
- Calculate the required throughput to meet production goals
- Consider variable speed options for flexibility in different scenarios
- Accumulation Patterns:
- Design appropriate accumulation and dispenser patterns
- Implement filer systems for smooth product flow
- Incorporate sensors to monitor and control accumulation rates
Material Selection
- Product Compatibility:
- Choose materials that are compatible with the products being handled
- Consider factors such as chemical resistance, durability, and cleanability
- Use food-grade materials for applications in the food and beverage industry
- Environmental Factors:
- Select materials that can withstand the operating environment
- Consider temperature resistance, humidity tolerance, and UV stability
- Implement coatings or layers to avoid corrosion or dust accumulation
Control Systems and Automation
- Sensor Integration:
- Incorporate sensors to detect product presence and accumulation levels
- Use indicators to show system status and accumulation progress
- Implement controls to manage product flow and prevent overflow
Maintenance and Accessibility
- Serviceability:
- Design for easy access to key components for maintenance
- Include removable parts or panels for cleaning and repairs
- Consider modular designs for quick replacement of worn components
- Cleaning Considerations:
- For food and pharmaceutical applications, design with sanitation in mind
- Implement CIP (Clean-in-Place) or COP (Clean-out-of-Place) features
- Avoid areas where product residue or dust can accumulate
Safety Features
- Guarding and Interlocks:
- Design appropriate guarding to protect operators
- Implement safety interlocks on access points
- Include emergency stop functions at key locations
- Ergonomics:
- Design control panels and HMIs for easy operator access
- Consider ergonomic factors for any manual interaction points
- Implement features to reduce repetitive motions and strain
Customization and Flexibility
- Modular Design:
- Create designs that allow for easy expansion or reconfiguration
- Consider future production needs and potential changes
- Design interfaces that allow integration with various upstream and downstream equipment
- Product Changeover:
- Implement features for quick and easy product changeovers
- Design adjustable guides and rails to accommodate different product sizes
- Consider tool-less adjustment features for operator convenience
Documentation and Support
- Technical Documentation:
- Provide comprehensive operation manuals and maintenance guides
- Include detailed parts lists for easy ordering of replacements
- Offer DWG files or 3D models for integration into plant layouts
- Training and Support:
- Develop training programs for operators and maintenance staff
- Offer ongoing technical support and troubleshooting guides
- Provide access to online resources, including videos and wikis
By carefully considering these design factors, manufacturers like Garvey can create accumulation tables that meet the specific needs of their customers while ensuring efficiency, reliability, and long-term value. The goal is to design a system that not only performs its primary function of accumulation but also integrates seamlessly into the broader production ecosystem, providing tangible benefits to the end-user.
Advanced Features and Technologies
The landscape of accumulation tables is rapidly evolving, with manufacturers incorporating cutting-edge technologies to meet the demands of modern production environments. These advancements not only improve efficiency but also offer unprecedented levels of control, data insights, and integration capabilities.
Sensor-Based Accumulation Control
Modern accumulation systems are equipped with sophisticated sensor arrays that provide real-time monitoring and control. These sensors can detect product presence, orientation, and even quality attributes, allowing for more precise accumulation management. For example:
- Optical sensors can detect the presence and position of products, even transparent items like glass bottles.
- Pressure sensors can measure the weight distribution on the table, ensuring optimal load balancing.
- Advanced vision systems can inspect products for defects as they accumulate, flagging items for removal.
These sensor systems are often linked to indicator panels that show the accumulation status, allowing operators to quickly assess the system’s performance at a glance.
Variable Speed Drives and Intelligent Motion Control
- Smoother product handling, reducing the risk of damage to delicate items like eggs or fragile electronics.
- Improved energy efficiency, as the system only operates at the required speed.
- Enhanced flexibility to handle varying product sizes and weights without manual adjustments.
Advanced motion control algorithms, often based on complex equations, ensure that products are moved with precision, reducing wear on both the conveyor components and the products themselves.
Energy-Efficient Designs
- Low-friction materials and coatings that reduce power requirements.
- Regenerative braking systems that capture and reuse energy during deceleration.
- Smart power management that puts sections of the conveyor into sleep mode when not in use.
These features not only reduce operating costs but also align with corporate sustainability goals, making them attractive to environmentally conscious buyers.
Integration with Industry 4.0 and IoT
- Built-in data collection and analysis capabilities, allowing for real-time performance monitoring and predictive maintenance.
- Integration with Manufacturing Execution Systems (MES) and Enterprise Resource Planning (ERP) software for seamless production planning and tracking.
- Remote monitoring and control capabilities, enabling off-site management and troubleshooting.
This level of integration allows manufacturers to treat their accumulation tables not as isolated units, but as part of a larger, interconnected production ecosystem.
Customization and Modularity
Recognizing that one size doesn’t fit all, leading manufacturers are offering highly customizable and modular designs. These systems can be tailored to specific industry needs, whether it’s for handling delicate electronic components or managing the flow of products in a busy kitchen environment. Modular designs allow for:
- Easy expansion or reconfiguration as production needs change.
- Quick replacement of parts for maintenance or upgrades.
- The ability to create custom layouts that fit existing factory floor plans.
This flexibility is particularly beneficial for companies that frequently change product lines or need to adapt to seasonal demand fluctuations.
Advanced User Interfaces and Training Tools
As accumulation systems become more sophisticated, so too do the interfaces used to control them. Modern systems often feature:
- Intuitive touchscreen controls that allow operators to quickly adjust settings and monitor performance.
- Augmented reality (AR) interfaces that overlay real-time data and control options onto a view of the physical system.
- Built-in training modules and simulations to help new operators get up to speed quickly.
Many manufacturers are also leveraging platforms like YouTube and internal wikis to provide ongoing support and training resources, ensuring that operators can always access the information they need to run the system effectively.
Predictive Maintenance and Self-Diagnostics
- Detect wear patterns and alert maintenance teams before failures occur.
- Perform self-diagnostics to identify potential issues early.
- Generate maintenance schedules based on actual usage rather than fixed intervals.
These features help to maximize uptime and extend the lifespan of the equipment, providing significant benefits to the end-user in terms of reduced maintenance costs and improved reliability.
In conclusion, the advancements in accumulation table conveyor technology are transforming these systems from simple material handling devices into sophisticated, data-driven components of the modern smart factory. As manufacturers continue to innovate, we can expect to see even more integration of AI, machine learning, and advanced materials, further enhancing the capabilities and efficiency of these crucial production tools.
Future Trends in Accumulation Tables
Smart Pricing and Sale Strategies
- Dynamic pricing models that adjust based on real-time market demand and raw material costs
- Subscription-based services where buyers pay for uptime rather than owning the equipment outright
- AI-powered sales configurators that help buyers dial in the perfect system for their needs
These strategies will make high-end accumulation systems more accessible to a wider range of businesses, potentially increasing market penetration.
Enhanced Internal Components
- Self-lubricating bearings that reduce maintenance needs and extend equipment life
- Advanced materials that resist deprecation, maintaining value over longer periods
- Modular designs allowing for easy upgrades, reducing the need for complete system replacement
These improvements will benefit buyers by lowering long-term ownership costs and improving system longevity.
Multilingual Interfaces
- Multilingual control panels that can switch between languages, including English, with a simple dial
- Voice-activated controls that understand multiple languages and dialects
- Augmented reality overlays that translate information in real-time for international operators
These features will make it easier for multinational companies to deploy and operate systems across various regions.
Advanced Coating Technologies
- Self-cleaning coats that repel dirt and product residue, maintaining a hygienic environment
- Anti-static layers that prevent product sticking, especially beneficial for handling items like plastic eggs
- Wear-resistant coatings that extend the lifespan of conveyor belts and rollers
These advancements will reduce maintenance needs and improve system reliability.
Data-Driven Optimization
The future of accumulation tables lies in their ability to collect and utilize data:
- AI algorithms that continuously optimize product flow, getting smarter with each production run
- Predictive maintenance systems that forecast potential failures before they occur
- Digital twins allowing for virtual testing and optimization of table configurations
By leveraging data, manufacturers can ensure their systems are always operating at peak efficiency.
Enhanced Product Handling
- Micro-zoning technology for precise product positioning and separation
- Adaptive surfaces that can change texture or shape to accommodate various products, from delicate eggs to robust packages
- Electromagnetic fields for contactless product movement, reducing wear and damage
These features will allow for gentler handling of delicate products while maintaining high throughput.
Energy Efficiency and Sustainability
- Energy recuperation systems that capture and reuse kinetic energy from conveyor motion
- Solar-powered options for facilities looking to reduce their carbon footprint
- Biodegradable components to minimize environmental impact when parts need replacement
These eco-friendly features will help companies meet sustainability goals while potentially reducing operating costs.
Integration with Robotics and Automation
- Collaborative robots working alongside human operators to manage product flow
- Integrated robotic arms for sorting and orientation tasks
- Mobile robots that can reconfigure accumulation table layouts based on production needs
This integration will create more flexible and adaptable production environments.
Enhanced Safety Features
- Advanced sensors detecting human presence and automatically adjusting operation
- Ergonomic designs reducing strain on operators during system interaction
- Integrated safety protocols that adapt to different product types and operating conditions
These safety enhancements will not only protect workers but also help companies comply with evolving regulations.
Customization and Modularity
- Modular designs allowing for quick reconfiguration to handle different product types
- 3D-printed components for rapid customization and replacement of parts
- Plug-and-play modules that can be easily added or removed to change system capabilities
This flexibility will benefit manufacturers by reducing downtime during product changeovers and enabling quick adaptation to new production requirements.
As these trends continue to develop, accumulation tables will evolve from simple material handling devices into sophisticated, intelligent systems. They’ll become central hubs in the smart factories of the future, populated with advanced technologies that were once the stuff of science fiction.
Manufacturers and buyers alike should stay informed about these advancements to ensure they can leverage the full benefits of next-generation accumulation technology. Whether you’re part of an established manufacturing LLC or a startup looking to revolutionize production, these trends will shape the future of material handling.
Choosing the Right Accumulation Table Conveyor
Assess Your Product Characteristics
The first step in choosing the right accumulation table conveyor is to thoroughly understand the products you’ll be handling:
- Size and shape: Are you dealing with small items like eggs or larger products?
- Weight: This will affect the load-bearing requirements of your conveyor.
- Fragility: Delicate items may require specialized handling features.
- Surface characteristics: Consider if your products need a specific coat or finish that could be affected by the conveyor surface.
For example, if you’re in the egg industry, you’ll need a conveyor with gentle handling capabilities and possibly a separator function to organize the eggs efficiently.
Evaluate Your Production Requirements
Consider your production needs and how they might evolve:
- Throughput: Calculate the volume of products you need to move per hour.
- Accumulation time: Determine how long products need to be accumulated.
- Line integration: Assess how the accumulation table will fit into your existing production line.
- Flexibility: Consider if you need to handle multiple product types or sizes repeatedly.
Use production data and forecasts to create a macro view of your needs, ensuring the system you choose can handle both current and future requirements.
Space and Layout Considerations
Your local facility constraints will play a crucial role:
- Available floor space: Measure the area where the accumulation table will be installed.
- Height restrictions: Consider vertical space if you’re looking at multi-level or spiral accumulators.
- Integration with existing equipment: Ensure the new system can seamlessly connect with your current setup.
Remember, a well-designed accumulation system can optimize your floor space, potentially freeing up room for other operations.
Budget and Financial Considerations
While price is a key factor, it’s important to consider the total cost of ownership:
- Initial investment: Compare upfront costs between different models and manufacturers.
- Operating costs: Consider energy efficiency and maintenance requirements.
- Longevity and depreciation: Look for systems that will maintain their value over time.
- Financing options: Some manufacturers offer leasing or financing plans, similar to a mortgage, which can help manage cash flow.
Develop a cost-benefit equation that takes into account both short-term and long-term financial impacts.
Technical Specifications and Features
Dive into the technical attributes of different systems:
- Speed control: Look for variable speed options for flexibility.
- Accumulation patterns: Consider if you need specific accumulation strategies.
- Material construction: Ensure the materials used are suitable for your products and environment.
- Control systems: Evaluate the user interface and integration capabilities with your existing systems.
Customization and Scalability
- Modular design: Look for systems that allow easy expansion or reconfiguration.
- Custom features: Assess if the manufacturer can provide industry-specific customizations.
- Future-proofing: Consider how easily the system can be upgraded as technology advances.
A flexible system can grow with your business, potentially saving you from having to replace the entire setup as your needs evolve.
Manufacturer Reputation and Support
The choice of manufacturer is as important as the conveyor itself:
- Track record: Research the manufacturer’s history and reputation in the industry.
- Customer support: Evaluate the level of after-sales service and technical support offered.
- Training: Consider the training provided for your operators and maintenance team.
- Spare parts availability: Ensure that replacement parts will be readily available when needed.
Look for manufacturers with a strong presence in your local area or industry sector for better support.
Trial and Testing
Before making a final decision:
- Request demonstrations: See the equipment in action, preferably with your own products.
- Run simulations: Use probability models to test how the system would perform under various scenarios.
- Pilot testing: If possible, arrange for a trial period or smaller-scale implementation.
This hands-on approach can provide valuable insights and confirm if the system meets your specific needs.
Industry-Specific Considerations
Different industries may have unique requirements:
- Food and beverage: Look for systems with hygienic design and easy-to-clean surfaces.
- Pharmaceuticals: Consider systems that can handle sterile environments and offer traceability features.
- E-commerce: Focus on flexibility to handle various product sizes, from small items like shoes to larger packages.
Ensure the chosen system complies with industry-specific regulations and best practices.
Garvey’s Patented Accumulation Table
Since 1926, Garvey has been synonymous with quality and innovation in the conveyor industry. Our journey from a small machine shop to a global leader in accumulation systems is a testament to our commitment to excellence and continuous improvement. To learn more about our rich history and how we can bring our expertise to your production challenges, visit our About Us page or contact a Garvey representative today.
Future-Proofing Your Investment
Finally, consider how your choice will stand the test of time:
- Technology compatibility: Ensure the system can integrate with emerging technologies in your industry.
- Sustainability features: Look for energy-efficient options that align with long-term sustainability goals.
- Adaptability: Choose a system that can handle potential changes in your product line or production processes.
By carefully considering these factors, you can select an accumulation table conveyor that not only meets your current needs but also positions your operation for future success. Remember, the right choice is not just about handling your products efficiently today, but about creating a flexible, scalable solution that will support your business growth for years to come.
Financial and Operational Analysis for Accumulation Table Conveyor Implementation
When considering the implementation of an accumulation table conveyor, it’s crucial to conduct a thorough financial and operational analysis. This process will help you understand the full impact of your investment and make an informed decision. Let’s explore the key aspects of this analysis.
Return on Investment (ROI) Calculation
To determine the financial viability of your accumulation table conveyor, you need to calculate the ROI:
- Initial Investment: Consider the purchase price and installation costs.
- Operational Savings: Estimate labor cost reductions and efficiency gains.
- Maintenance Costs: Factor in regular maintenance and potential repairs.
- Lifespan: Consider the expected lifespan of the equipment to calculate long-term value.
What specific financial attributes of your operation will be impacted by this implementation? This question is crucial in determining the true ROI.
Financing Options
Explore various financing options to fund your accumulation table conveyor:
- Outright Purchase: If you have the capital, this might be the most cost-effective long-term option.
- Leasing: This can be a good option if you want to conserve cash flow.
- Equipment Loans: Similar to a mortgage, these loans allow you to spread the cost over time.
Consider how each option will turn your current financial situation and impact your cash flow.
Operational Efficiency Analysis
Conduct a detailed analysis of how the accumulation table conveyor will affect your operations:
- Throughput Increase: Calculate the expected increase in production capacity.
- Labor Reallocation: Determine how many person-hours can be reallocated to other tasks.
- Quality Improvement: Estimate the reduction in product damage or defects.
- Downtime Reduction: Project the decrease in production line stoppages.
Use probabilistic models to account for variations in these factors and create a range of potential outcomes.
Risk Assessment
Every implementation comes with risks. Identify and quantify potential risks:
- Implementation Delays: What’s the probability of delays and their potential impact?
- Performance Issues: Consider the likelihood of the system not meeting expected performance metrics.
- Market Changes: How might shifts in your market affect the value of this investment?
- Regulatory Changes: What potential regulatory changes could impact the use or value of the system?
Develop contingency plans for each identified risk to ensure you’re prepared for various scenarios.
Scalability and Future-Proofing
Consider how the accumulation table conveyor will adapt to your future needs:
- Growth Projections: How will the system handle increased production volumes?
- Product Changes: Will the system be able to accommodate new products or packaging?
- Technology Integration: How easily can the system integrate with emerging technologies?
This analysis will help ensure that your investment remains valuable as your business evolves.
Total Cost of Ownership (TCO) Analysis
Look beyond the initial purchase price to understand the true cost over the system’s lifetime:
- Energy Costs: Calculate the expected energy consumption and associated costs.
- Maintenance Expenses: Project routine maintenance costs and potential major repairs.
- Training Costs: Factor in initial and ongoing training for operators and maintenance staff.
- Upgrade Costs: Consider potential future upgrades to keep the system current.
A comprehensive TCO analysis will give you a clearer picture of the long-term financial implications.
Operational Impact Assessment
Consider how the new system will affect your overall operations:
- Workflow Changes: How will existing processes need to change?
- Staff Retraining: What training will be required for your team to operate the new system?
- Space Utilization: How will the new system impact your facility’s layout?
- Integration with Existing Systems: What modifications might be needed to integrate with your current setup?
This assessment will help you prepare for the operational changes that come with the new system.
By conducting this comprehensive financial and operational analysis, you’ll be well-equipped to make an informed decision about implementing an accumulation table conveyor.
Remember, the goal is not just to understand the costs and benefits, but to gain a clear picture of how this investment will turn your operations and financial position in both the short and long term.
What unique aspects of your business need to be considered in this analysis? By addressing this question, you’ll ensure that your analysis is tailored to your specific situation and needs.
Garvey - Your Partner for Accumulation Tables
Frequently Asked Questions (FAQs) about Garvey Accumulation Tables
What is an accumulation table, and how does it differ from a standard conveyor?
How do I determine which Garvey accumulation system is right for my production line?
To choose the right system:
- Assess your product characteristics (size, shape, weight)
- Evaluate your production requirements (throughput, accumulation time)
- Consider your space constraints
- Analyze your specific industry needs
Consult with a Garvey expert for personalized recommendations.
Can Garvey accumulation tables handle fragile or irregularly shaped products?
Yes. Garvey’s Infinity™ technology uses patented loop technology to handle even the most unstable products with zero back pressure, minimizing product damage.