Line Analysis
Maximize your Production
How does an accumulator increase throughput?
Consider the following example: Bottles are coming out of the filler, getting capped, and then going directly to a labeler on a conveyor. Everything is running smoothly until the roll of labels needs to be replaced. You stop the labeler to remove the empty spool and replace it with a new one. This action only takes a minute or two but during this changeover the bottles back up in front of the labeler and cause the filler to stop. In fact, every time a machine downstream of the filler stops, the filler does as well.
The filler is usually the slowest and most expensive machine in the production line, so it is important to maximize its uptime by not letting other machine stoppages affect it. Placing an appropriately sized accumulator between the filler and the rest of the production creates a buffer zone to accumulate product when machines down the line are stopped, thus protecting the filler and allowing it to continue running. Now, when the labeler is down, the filler keeps on going and begins to fill the accumulator. When the labeler is back up and running, it empties the accumulator back out again making it ready for the next downstream stoppage. Adding an accumulator can dramatically increase the overall throughput of the entire production line.
The previously described scenario is a simple example that shows the clear benefit of accumulation. The graphics below illustrate how an expert line analysis and two accumulation tables improved throughput by over 28 percent!
Production Line Analysis
Without Accumulation
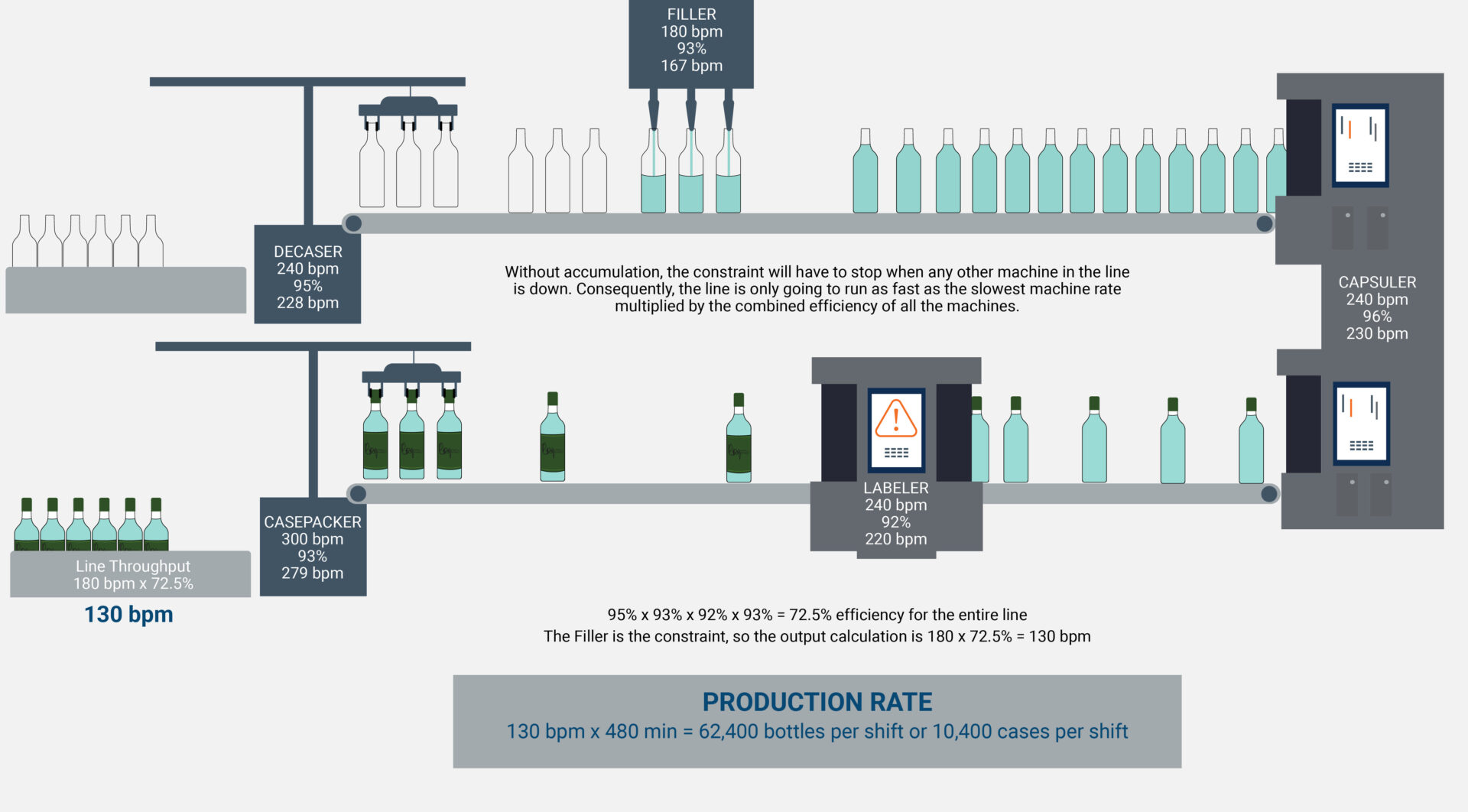
Adding Single Accumulation System
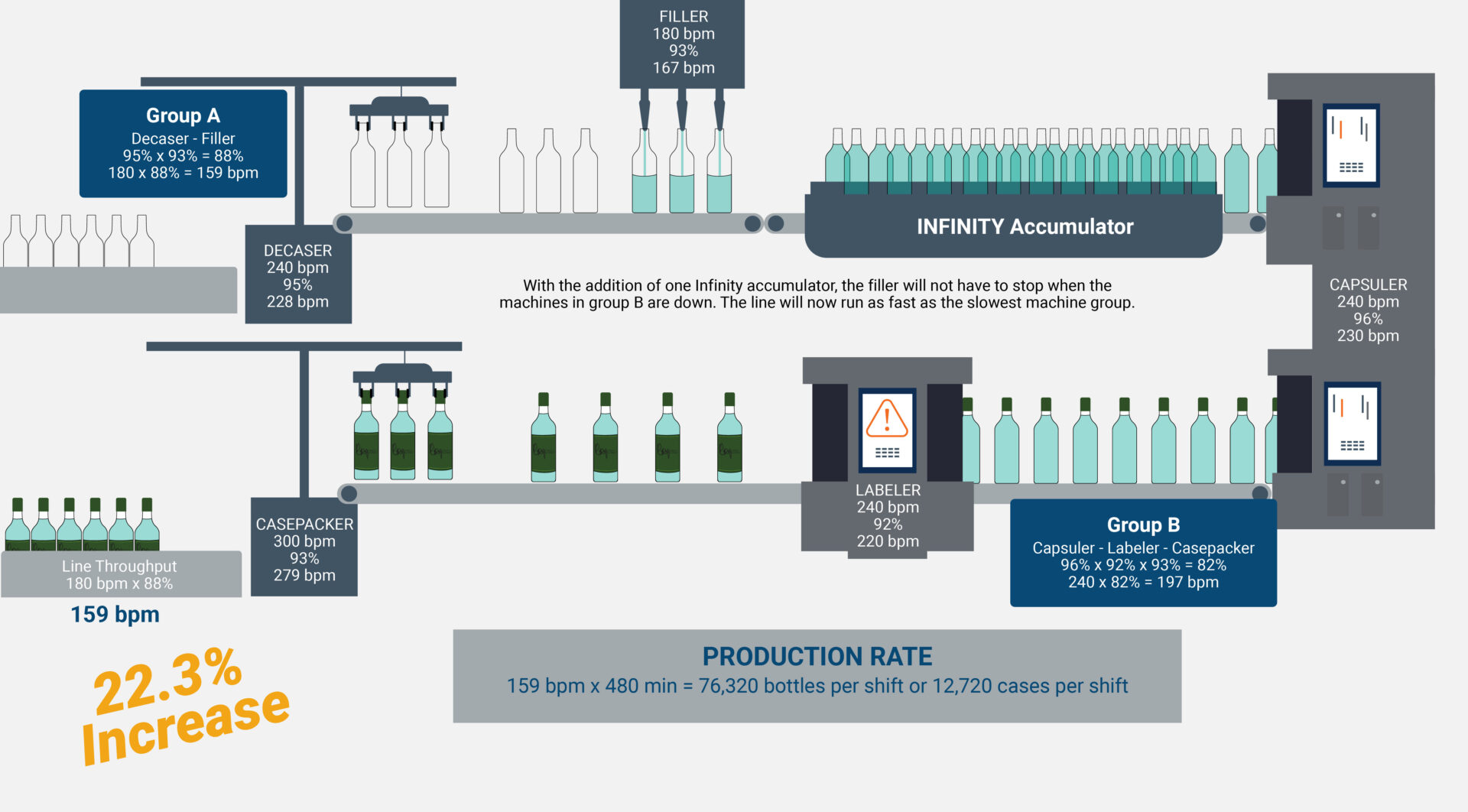
Optimal Accumulation Solution
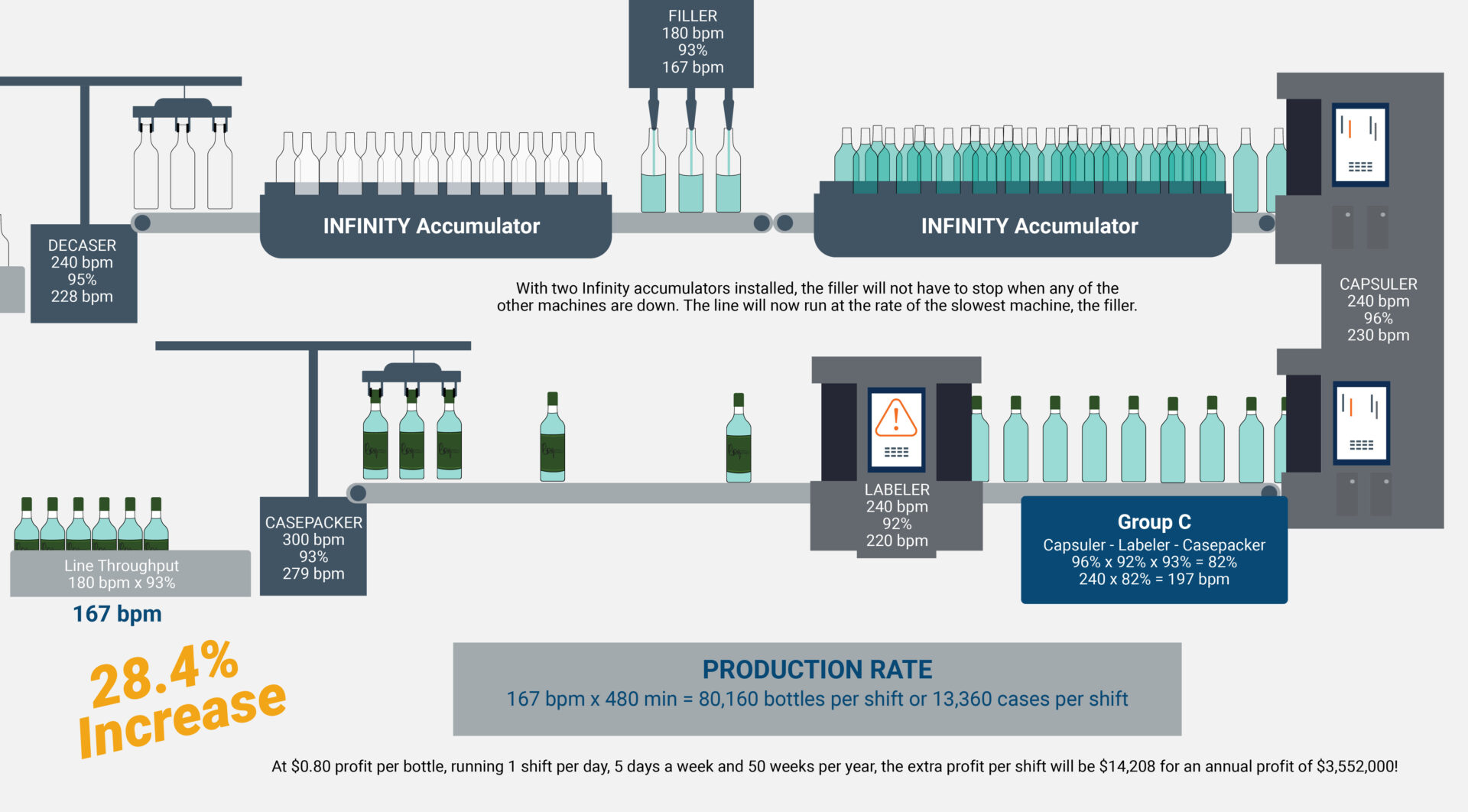
How do I know if I need accumulation?
Every production line has a constraint. If downtime on other machines causes the constraint to shut down, you will benefit from accumulation.
What size/type of accumulation table do I need?
The accumulation size should be equal to the machine with the longest average repair time on the line, other than the constraint.
Can a Garvey representative take a look at my production line and make recommendations?
Sure! Our sales engineers would love to stop by your facility and conduct a free line analysis. Visit our contact page for more information.