Table Top Conveyor Solutions
Are production line inefficiencies limiting your throughput?
Discover How Garvey’s Table Top Conveyor Solutions Can Transform Your Manufacturing Process.
Imagine a production line where products flow seamlessly from start to finish, with precise handling and zero pressure damage. From delicate glass vials to heavy containers, from round bottles to rectangular cartons, our table top conveyor systems ensure flawless product transport at every stage of your operation.
Whether you need FDA-compliant sanitary design for food processing or robust industrial solutions for high-speed packaging, we can handle it. Our nearly century-long legacy of innovation means one thing: when standard conveyors fail, Garvey delivers.
Why Choose Garvey Table Top Conveyors?
Our patented conveyor technology delivers what standard table top systems can’t:
Precision Product Handling
- Zero-pressure transport eliminates product and label damage
- Handles any shape – from round bottles to rectangular cartons
- Maintains perfect product orientation
Advanced Line Integration
- Seamless integration with existing equipment
- Multiple configurations for 90° and 180° transfers
- Custom solutions for unique space requirements
Industry-Leading Support
- Free in-house product testing
- Complete line analysis
- Expert technical support
Sanitary Design Standards
- Stainless steel construction for washdown environments
- Tool-free maintenance access
- FDA and USDA compliant design
Proven Experience
- Nearly 100 years of conveyor innovation
- Trusted by leading manufacturers worldwide
- Multiple patents and ongoing R&D
Explore Our Range of Table Top Conveyors
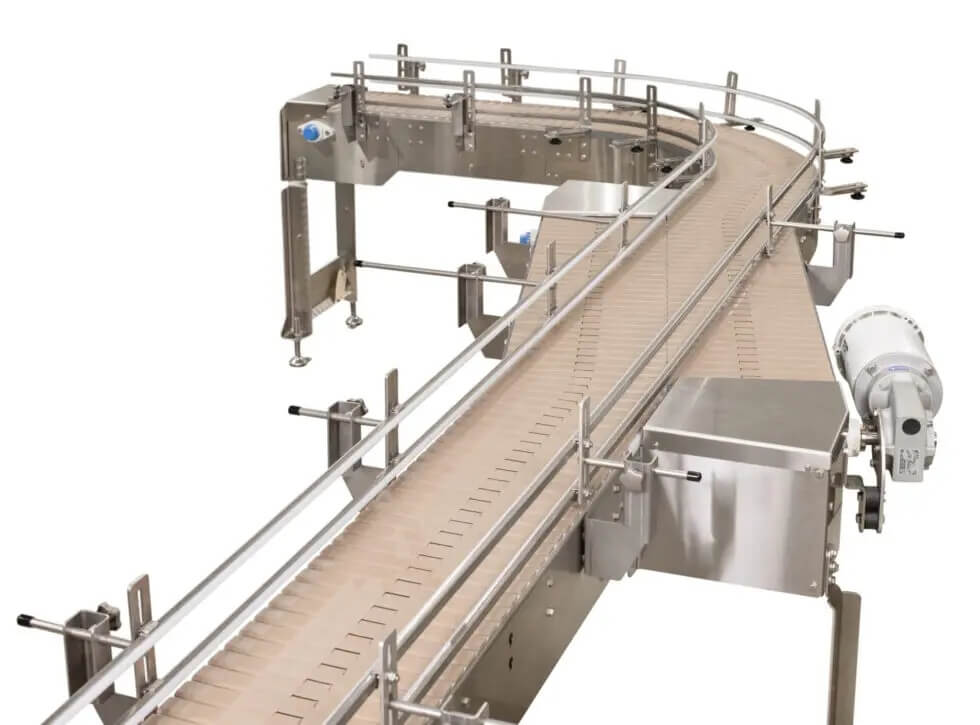
AquaGard GT Series Conveyor
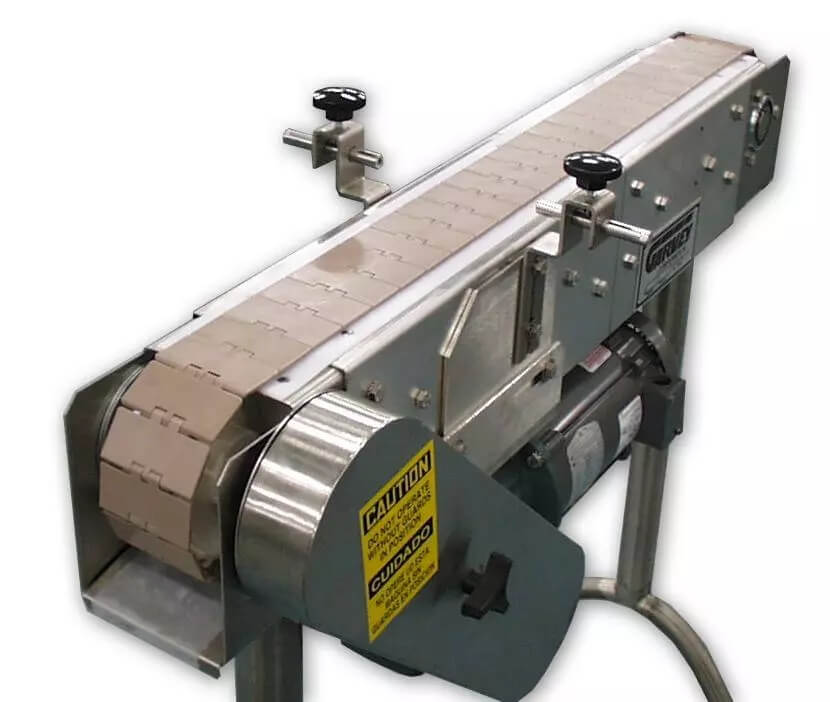
9600 Series Table Top Conveyor
Take the Next Step in Optimizing Your Production Line
We understand every production line is unique. Let us show you how our solutions can address your specific challenges.
Transform your manufacturing efficiency today with Garvey’s table top conveyor solutions.
Introduction to Table Top Conveyors
From dairy products to glass bottles, modern table top conveyor systems handle diverse materials. These conveyor chains excel in transporting everything from lightweight plastic containers to heavy cartons, making them ideal for food, beverage, and manufacturing applications.
What Are Table Top Conveyors?
A table top conveyor system consists of a continuous chain mechanism that moves along a steel table frame, creating a stable, flat surface for product transport. Unlike standard conveyor belt systems, table top chain conveyors utilize specialized plastic or stainless steel chains that provide smooth, consistent product handling capabilities.
These systems can be configured in multiple layouts, including:
- Straight-run configurations
- 90-degree angle conveyor turns
- 180-degree conveyor returns
- Custom curved sections for specific applications
Key Components
Modern table top conveyor systems integrate several crucial components:
-
Chain Assembly
- Plastic table top chains for general applications
- Stainless steel table top chains for sanitary environments
- Modular chain designs for easy maintenance
- Specialized sprocket systems for smooth operation
-
Frame Construction
- Robust steel table frames for industrial durability
- Sanitary stainless steel table designs for food and pharmaceutical use
- Horizontal frame configurations for standard transport
- Custom frame heights for ergonomic integration
-
Drive Systems
- Energy-efficient conveyor belt motors
- Variable speed control options
- Portable power supplies for flexible layouts
- Washdown-rated components for cleaning requirements
-
Guide Rails and Accessories
- Adjustable conveyor table rails
- Product orientation guides
- Modular rail systems for different product sizes
- Quick-change components for rapid changeover
Table top conveyors excel in applications requiring precise product handling and accumulation capabilities. Whether transporting small bottles, rigid containers, or packaged goods, these systems provide reliable performance while protecting product integrity throughout the manufacturing process.
Common applications include:
- Food and beverage processing
- Pharmaceutical manufacturing
- Consumer goods packaging
- Industrial assembly operations
The versatility of table top conveyor systems makes them ideal for both standalone operations and integration into larger automated production lines, where they can be configured with various angles and return paths to optimize floor space utilization.
By understanding the fundamental components and capabilities of table top conveyor systems, manufacturers can better evaluate their material handling needs and select the appropriate configuration for their specific applications.
The Benefits of Table Top Conveyors
From carton handling to bottle transport, modern table top conveyor systems serve diverse needs. Whether integrating with pallet systems, elevators, or rotary tables, these machines form the backbone of efficient production lines. The versatility extends to handling various products including liquids, snacks, candy, boxed items, and more.
Table Top Conveyor Comparisons: Understanding Your Options
Table Top vs. Mat Top Conveyors
Table top conveyor systems and mat top conveyors each serve specific purposes in industrial applications. Table top chain conveyors typically feature individual links that create a flat surface, while mat top designs utilize a continuous belt-like surface.
Key Differentiators:
- Surface Characteristics
- Load Capacity
- Maintenance Requirements
- Application Flexibility
Table Top Advantages:
- Superior product stability
- Enhanced orientation control
- Better suited for 90-degree and 180-degree turns
- Easier component replacement
- Optimal for accumulation
Mat Top Benefits:
- Smoother product transfer
- Reduced noise levels
- Fewer moving parts
- Better for loose materials
- Lower initial cost
Table Top vs. Belt Conveyors
The choice between a table top conveyor system and traditional conveyor belt designs often depends on specific application requirements and environmental conditions.
Traditional belt conveyors excel in:
- Bulk material handling
- Long straight runs
- Simple installations
- Lower maintenance costs
Table top chain conveyors provide advantages in:
- Precise product positioning
- Complex routing requirements
- Wash-down environments
- High-speed applications
Table Top vs. Roller Conveyors
While both systems serve important roles in material handling, they offer distinct operational characteristics:
Table Top Benefits:
- Better product stability
- Improved control at transfers
- Superior for small items
- Enhanced accumulation capabilities
Roller Conveyor Advantages:
- Lower power consumption
- Simplified maintenance
- Better for heavy loads
- Easier manual manipulation
Table Top vs. Plastic Modular Belt
The decision between table top and plastic modular belt systems often comes down to specific application requirements:
Table Top Applications:
- High-precision handling
- Complex routing needs
- Speed-sensitive operations
- Clean room environments
Modular Belt Uses:
- Food processing
- Wet environments
- Heavy-duty applications
- Temperature extremes
Making the Right Choice
When selecting between different conveyor types, consider:
-
Product Characteristics
- Size and weight
- Surface texture
- Temperature requirements
- Fragility concerns
-
Operational Requirements
- Speed needs
- Cleaning protocols
- Maintenance capabilities
- Environmental conditions
-
Facility Considerations
- Available space
- Layout requirements
- Integration needs
- Budget constraints
Understanding these differences helps manufacturers select the optimal conveying solution for their specific needs. The right choice depends on a thorough analysis of your unique requirements, including:
- Production volume
- Product characteristics
- Environmental conditions
- Maintenance capabilities
- Long-term operational costs
By carefully evaluating these factors against each conveyor type’s strengths and limitations, manufacturers can make informed decisions that optimize their material handling operations and support long-term production goals.
Technical Specifications and Design Considerations
Understanding the technical aspects of table top conveyor design is crucial for selecting the right equipment for your specific manufacturing needs. From basic conveyor parts to specialized design features, each component plays a vital role in system performance.
Construction Materials and Standards
-
Metal Framework Options
- Heavy-duty steel construction for industrial applications
- Vacuum-sealed stainless steel for sterile environments
- Double-stack designs for maximizing vertical space
- Custom lift and turn sections for elevation changes
-
Chain Specifications
- Standard C2060 chains for general applications
- Specialized bottle handling chains
- High-temperature chains for oven integration
- Custom designs for unique product requirements
Dimensional Considerations
- Standard inch measurements for North American specifications
- Variable width options (ranging from small bottle handling to large pizza ovens)
- Hydraulic lift mechanisms for height adjustability
- Roller transfer sections for smooth product handling
Industry-Specific Equipment Options
Food Processing
- Pizza conveyor ovens with infrared heating
- Sushi conveyor systems with precise temperature control
- 120V compatible systems for standard power requirements
- Washable components for sanitary maintenance
Industrial Manufacturing
- Reflow ovens for electronics assembly
- Screen printing integration capabilities
- Furnace-compatible conveyor designs
- AR300 grade materials for high-temperature applications
Cost Considerations
- New vs. used equipment options
- Supplier reputation and support services
- Parts availability and maintenance costs
- Total lifecycle value analysis
Many manufacturers offer cost-effective solutions without sacrificing quality:
- Standard designs for budget-conscious projects
- Modular systems for scalable implementation
- Refurbished options from reputable suppliers
- Direct-from-manufacturer pricing
Integration Capabilities
- Scissor lift mechanisms for elevation changes
- Step file compatibility for CAD design integration
- Multiple stack configurations
- Existing production equipment
- Intralox transfer systems
- Timing belt transitions
- Pneumatics systems
- Elevator mechanisms
- Rotary table interfaces
- Heat tunnels
- Sealers and printersInkjet printing stations
- Wire guide systems
- Screw feed mechanisms
Supplier Selection
- Manufacturing expertise and history
- Parts availability and support
- Custom design capabilities
- Technical documentation and resources
Leading manufacturers provide comprehensive support including:
- Detailed technical specifications
- CAD files for integration planning
- Installation guidelines
- Maintenance documentation
Understanding these technical specifications and design considerations ensures optimal system selection and implementation, leading to improved operational efficiency and return on investment.
Advanced Features and Technologies
These advancements represent a significant leap forward in manufacturing automation, particularly in pressure-sensitive product handling and smart system integration.
System Construction and Integration
Construction flexibility allows for complex configurations including:
- Curved sections for space optimization
- Carbon steel and stainless steel builds
- Metal and plastic component options
- Custom extrusion designs
- Tool-free maintenance access points
Modern conveyor equipment often integrates specialized tools like:
- Inkjet printing systems
- Heat tunnels and sealers
- Wire guide mechanisms
- Intralox transfer solutions
- Rotary table interfaces
Accumulation Systems and Methods
Pressureless accumulation technology has revolutionized the way products move through production lines. Unlike traditional conveyor systems, advanced accumulation solutions prevent product damage while maintaining continuous flow.
Key accumulation features include:
- Zero-pressure product handling
- Dynamic flow control algorithms
- Automatic speed synchronization
- Multi-zone accumulation capabilities
The integration of these features ensures products can accumulate without the risk of crushing or damage, particularly crucial in industries handling delicate items like glass bottles or sensitive electronic components.
Automation Control Systems
Modern control architectures provide unprecedented operational visibility and control:
Smart Monitoring Features
- Real-time throughput tracking
- Predictive maintenance alerts
- Energy consumption monitoring
- Performance optimization data
Integration Capabilities
- PLC integration protocols
- Industry 4.0 compatibility
- Remote monitoring systems
- Custom API implementations
The seamless integration of these control systems allows manufacturers to optimize their operations continuously, reducing downtime and improving overall equipment effectiveness (OEE).
Advanced Motion Control
- Precision Movement
- Variable speed control
- Soft start/stop capabilities
- Dynamic load balancing
- Synchronized multi-conveyor operation
- Energy Management
- Smart power consumption
- Regenerative braking systems
- Load-based power optimization
- Energy usage monitoring
These advanced motion control features work together to ensure smooth product handling while maximizing energy efficiency and reducing operational costs.
Quality Assurance Integration
- Vision system integration
- Weight verification stations
- Metal detection capabilities
- Barcode scanning systems
The seamless integration of these technologies transforms table top conveyors from simple transport systems into comprehensive quality control solutions that maintain product integrity throughout the production process.
The combination of these advanced features and technologies creates a robust, intelligent conveying system that not only moves products efficiently but also provides valuable operational insights and quality control capabilities. This technological integration is essential for manufacturers looking to optimize their production lines and maintain competitive advantages in today’s fast-paced manufacturing environment.
Successful implementation of these advanced features requires careful consideration of specific application requirements and thorough integration planning. When properly configured, these systems can significantly improve production efficiency while reducing operational costs and maintenance requirements.
Industry-Specific Applications for Table Top Conveyor Systems
Food and Beverage Manufacturing Applications
Sanitary Conveyor Requirements
- Stainless steel table top construction
- Washdown-rated components
- Sanitization-friendly plastic table top chains
- USDA/FDA-compliant materials
Food and beverage manufacturers rely on these systems for:
- Cheese and dairy product handling
- Carton handling systems
- Glass bottle and drink container transport
- Snack and candy processing
- Meat packaging operations
- Pizza conveyor oven systems for commercial bakeries
- Sushi conveyor belt installations for restaurants
- Horizontal conveyor systems for snack food production
- And more
Contract Packaging Operations
System Requirements
- Quick changeover capabilities
- Modular design for reconfiguration
- Multiple product size handling
- Integration with various packaging machines
Critical features include:
- Adjustable guide rail systems
- Tool-less changeover mechanisms
- Universal product handling
- Mobile conveyor sections
Pharmaceutical and Medical Device Manufacturing
Critical Features:
- Clean room compatible stainless steel table construction
- Validation-ready components
- 90-degree and 180-degree conveyor configurations
- GMP-compliant conveyor parts and materials
Typical applications in pharmaceutical manufacturing:
- Sterile vial handling systems
- Blister pack conveyance
- Medical device assembly lines
- Laboratory automation equipment
Pet Health Product Manufacturing
Essential Features
- Clean-room compatible materials
- Product orientation control
- Multiple container size handling
- Integration with filling equipment
Common uses include:
- Veterinary medicine packaging
- Pet food container transport
- Supplement bottle handling
- Medical device assembly
Consumer Goods Packaging
Key System Requirements
- High-speed accumulation capabilities
- Multiple conveyor angle options
- Flexible guide rail systems
- Quick-change product handling parts
Packaging line configurations often include:
- Multi-lane distribution systems
- Return conveyor loops
- Automatic product orientation
- Integrated quality control stations
Industrial Manufacturing Applications
Essential Features:
- Durable Construction
- Steel table frame designs
- Heavy-duty conveyor chains
- Industrial-grade drive components
- Reinforced support structures
- Process Integration
- Reflow oven conveyor systems
- Screen printing line integration
- Metal detection capabilities
- Infrared heating applications
The success of these industry-specific applications depends on selecting the right conveyor manufacturer who understands unique sector requirements. Whether implementing a small table top conveyor for lightweight products or designing complete conveyor systems for complex production lines, proper specification and configuration are essential.
Manufacturing facilities across these industries benefit from modern table top conveyor technology through:
- Increased throughput capacity
- Reduced product damage
- Improved operational efficiency
- Enhanced quality control capabilities
Visit our Industrial Industry Page
When selecting industrial conveyor equipment, manufacturers should consider both current requirements and future expansion needs to ensure their investment provides long-term value and scalability.
Performance Optimization for Table Top Conveyor Systems
Table Top Chain Conveyor Maintenance
Essential Maintenance Tasks:
- Regular chain tension inspection
- Conveyor belt alignment checks
- Sprocket wear monitoring
- Guide rail adjustment verification
System Performance Factors
- Bearing quality and maintenance schedules
- Chain conveyor tension and alignment
- Pneumatics system efficiency and pressure
- Voltage requirements for integrated equipment
- Transport speed optimization
- Friction coefficient management
These factors directly impact:
- Product flow consistency
- Energy consumption
- System longevity
- Maintenance frequency
Steel Table Top and Plastic Table Top Considerations
Steel Table Construction
- Regular surface inspection
- Proper lubrication schedules
- Corrosion prevention
- Weight distribution monitoring
Plastic Table Components
- Temperature monitoring
- UV exposure management
- Chemical compatibility checks
- Wear pattern analysis
90-Degree and 180-Degree Conveyor Optimization
Transfer Point Considerations:
- Smooth product transition
- Proper angle conveyor alignment
- Speed matching at transitions
- Guide rail positioning
Energy Efficiency Improvements
- Operational Optimization
- Variable speed control implementation
- Load-based power management
- Start/stop sequence optimization
- Peak demand reduction strategies
- Equipment Updates
- Energy-efficient motor upgrades
- Low-friction chain components
- Smart control system integration
- LED indicator implementation
Top Chain Conveyor Performance Metrics
- Throughout rates
- Energy consumption
- Maintenance frequency
- Downtime incidents
- Product damage rates
Used Table Top System Enhancement
- Component upgrade opportunities
- Modern control system integration
- Preventive maintenance scheduling
- Performance baseline establishment
The key to optimizing table top conveyor performance lies in systematic monitoring and proactive maintenance. By implementing these strategies, manufacturers can:
- Extend equipment lifespan
- Reduce operational costs
- Improve production efficiency
- Minimize unexpected downtime
Regular assessment and adjustment of these optimization strategies ensures continuous improvement in system performance and reliability. This approach helps maintain peak efficiency while reducing total cost of ownership for your conveyor table top installation.
Selection and Implementation Guide for Table Top Conveyors
Assessing Your Table Top Chain Requirements
Product Specifications
- Size and weight requirements
- Material composition
- Temperature sensitivity
- Surface characteristics
Production Environment Factors
- Available floor space
- Ambient conditions
- Sanitation requirements
- Integration points with existing equipment
Stainless Steel vs. Plastic Table Top Selection
Stainless Steel Table Top Benefits:
- Superior durability
- Enhanced load capacity
- Optimal for washdown environments
- Extended service life
Plastic Table Top Advantages:
- Cost-effective implementation
- Reduced noise levels
- Lower maintenance requirements
- Lighter weight construction
Conveyor Belt and Chain Configuration
- Chain Selection Criteria
- Load requirements
- Speed specifications
- Environmental conditions
- Maintenance accessibility
- Drive System Requirements
- Motor specifications
- Power availability
- Control system integration
- Emergency stop considerations
Degree Angle and Layout Planning
Common Configurations
- Straight-run conveyors
- 90-degree angle conveyor turns
- 180-degree conveyor returns
- Custom angle configurations
Special considerations include:
- Product orientation requirements
- Transfer point specifications
- Accumulation needs
- Operator access points
Implementation Strategy Development
- Pre-Installation
- Site preparation requirements
- Utility specifications
- Safety considerations
- Training requirements
- Installation Process
- Equipment positioning
- Power connection protocols
- Control system integration
- Testing procedures
- Post-Installation
- Operator training programs
- Maintenance schedules
- Performance monitoring
- System optimization
Return on Investment Calculation
- Initial equipment costs
- Installation expenses
- Operational savings
- Maintenance requirements
- Productivity improvements
- Energy efficiency gains
Success in selecting and implementing a table top conveyor system depends on thorough planning and attention to detail throughout the entire process. By carefully considering each aspect of the selection and implementation process, manufacturers can ensure their investment delivers the expected operational benefits and financial returns.
Regular review and adjustment of the implementation strategy ensures continuous improvement and optimal system performance throughout the equipment’s lifecycle.
Line Balancing & Efficiency in Table Top Conveyor Systems
Calculating Optimal Line Speeds
Key considerations for table top conveyor speed optimization:
- Calculate theoretical maximum speed using the formula: Optimal Line Speed = (Required Throughput × Product Length) / (60 × Product Spacing Factor)
- Account for product stability requirements specific to your table top chain configuration
- Consider acceleration and deceleration zones, particularly at conveyor transfer points
- Factor in operator interaction points along the conveyor table
- Analyze upstream and downstream equipment constraints
- Monitor actual throughput against theoretical maximums
- Implement variable speed controls for dynamic adjustment
The success of your table top conveyor system depends largely on finding the sweet spot between maximum throughput and stable product handling. Remember that faster isn’t always better – optimal speed considers multiple factors including product characteristics, line configuration, and operational requirements.
Managing Product Spacing on Table Top Conveyors
Critical spacing management elements include:
- Implementation of minimum gap control systems using photoelectric sensors
- Dynamic spacing calculations based on product dimensions and conveyor speed
- Strategic unscrambling solutions for optimal product orientation and spacing
- Strategic placement of spacing control mechanisms at key points along the conveyor table
- Integration of smart controls for automatic gap adjustment
- Regular monitoring and adjustment of spacing parameters
- Installation of accumulation zones for managing product flow
- Consideration of product-specific spacing requirements
When properly implemented, effective spacing management on your table top conveyor can significantly improve line efficiency while reducing product damage and downtime. Many modern table top conveyor manufacturers offer integrated spacing control solutions that can be customized to your specific application.
Reducing Bottlenecks in Table Top Conveyor Systems
Essential bottleneck reduction strategies include:
- Implementation of smart accumulation tables at critical transition points
- Installation of buffer zones before high-demand operations
- Strategic placement of parallel processing stations for bottleneck operations
- Integration of real-time monitoring systems for throughput analysis
- Optimization of conveyor merge and divert points
- Use of variable speed controls for flow management
- Regular analysis of throughput data to identify emerging constraints
- Implementation of preventive maintenance schedules
Successfully managing bottlenecks in your table top conveyor system requires a combination of proper planning, strategic equipment placement, and ongoing monitoring. Many modern table top conveyor manufacturers now offer integrated solutions specifically designed to address common bottleneck challenges.
Buffer Zone Planning for Table Top Conveyor Efficiency
Key buffer zone planning considerations:
- Calculate required buffer capacity using the formula: Buffer Size = (Downstream Downtime × Upstream Rate) + Safety Factor
- Strategic placement of accumulation zones before critical equipment
- Implementation of First In, First Out (FIFO) principles
- Design considerations for product-specific accumulation limits
- Integration of smart controls for buffer management
- Installation of jam detection and resolution systems
- Proper spacing for operator access and maintenance
- Emergency clearing procedures and protocols
Modern table top conveyor installations benefit from sophisticated buffer zone management systems that can automatically adjust to changing production conditions while maintaining optimal product flow and reducing the risk of damage.
Synchronizing Multiple Table Top Conveyor Speeds
Critical speed synchronization elements:
- Implementation of master control systems for coordinated operation
- Integration of dynamic speed adjustment capabilities
- Calculation of optimal speed ratios for transfer points
- Development of acceleration and deceleration profiles
- Installation of feedback loops for real-time adjustment
- Monitoring systems for speed verification
- Emergency stop coordination across multiple conveyors
- Integration with upstream and downstream equipment
The success of a multi-conveyor table top system depends largely on proper speed synchronization. Modern table top conveyor manufacturers offer sophisticated control systems that can maintain optimal speed relationships while adapting to changing production requirements.
Safety & Compliance in Table Top Conveyor Operations
Essential safety and compliance elements:
- Adherence to OSHA standards for conveyor operation
- Implementation of comprehensive guard systems
- Installation of emergency stop devices
- Development of operator training programs
- Regular safety audits and inspections
- Documentation of safety procedures
- Compliance with industry-specific regulations
- Integration of modern safety technologies
Understanding and implementing proper safety measures isn’t just about regulatory compliance – it’s about protecting your most valuable assets while maintaining efficient operation of your table top conveyor system.
Environmental Considerations for Table Top Conveyor Systems
Critical environmental control measures:
- Implementation of climate control systems
- Integration of dust and debris management solutions
- Installation of static control devices
- Management of temperature variations
- Control of humidity levels
- Protection against chemical exposure
- Noise reduction strategies
- Ventilation system integration
Modern table top conveyor installations must account for environmental factors to ensure reliable operation and extended equipment life. Many manufacturers now offer specialized solutions designed specifically for challenging environmental conditions.
Testing & Validation for Table Top Conveyor Systems
Essential testing and validation procedures:
- Implementation of thorough acceptance testing protocols
- Development of performance validation methods
- Integration of quality control systems
- Regular speed and load testing
- Stress testing under various conditions
- Documentation of test results
- Preventive maintenance scheduling
- Ongoing performance monitoring
The success of your table top conveyor installation depends largely on proper testing and validation procedures. Modern conveyor systems offer integrated monitoring and testing capabilities that help maintain optimal performance while identifying potential issues early.
Remember that successful implementation of these strategies requires ongoing commitment to monitoring, maintenance, and optimization. Many table top conveyor manufacturers offer support services to help you maximize the effectiveness of your installation while maintaining safe and efficient operation.
Future Trends and Innovations in Table Top Conveyor Technology
Smart Table Top Chain Systems
Key smart features include:
- Integrated sensor networks
- Real-time performance monitoring
- Predictive maintenance algorithms
- Remote diagnostic capabilities
Sustainable Manufacturing Solutions
Modern sustainable features emphasize:
- Advanced energy recovery systems
- Eco-friendly component materials
- Reduced friction design elements
- Smart power management protocols
Integration with Industry 4.0
The marriage of traditional conveyor functionality with advanced digital capabilities has created systems that can adapt in real-time to changing production requirements. Machine learning algorithms continuously analyze performance data, automatically adjusting operating parameters to maintain optimal efficiency while reducing energy consumption and wear.
Critical integration elements include:
- IoT sensor networks
- Cloud-based monitoring systems
- AI-powered optimization
- Automated maintenance scheduling
Emerging Applications and Market Evolution
As market demands evolve, table top conveyor technology continues to adapt. Manufacturers are developing increasingly specialized solutions for:
- High-precision electronics assembly
- Sterile medical device production
- Sustainable packaging operations
- Advanced pharmaceutical manufacturing
Looking Ahead
The ongoing development of table top conveyor technology reflects a broader shift toward smarter, more sustainable manufacturing practices. By embracing these innovations, manufacturers can:
- Optimize operational efficiency
- Reduce environmental impact
- Improve product quality
- Enhance production flexibility
As we look to the future, it’s clear that table top conveyor systems will continue to play a crucial role in shaping the future of industrial automation, driven by advances in technology and changing market demands.