Accumulation tables and conveyors all serve the same general purpose: keeping the line running without interruption. Accumulation ensures your machines always have a steady supply of product to process by providing buffers so that even if one machine goes down, e.g., a labeler runs out of paper, the rest of the line keeps working. (Accumulation systems may also be used to reorient, single-file, double-file, route products to other machines, etc., but the objective is still the same — keeping lines running.)
But just because accumulators have a common purpose doesn’t mean they’re all created equal. There are many different options available in terms of how the accumulation is accomplished.
We focus on standardized products because we believe, to quote Hunter S. Thompson, “Anything worth doing, is worth doing right.” Here are three key features that make Garvey’s accumulation tables and conveyors the best there is.
Pressureless loop technology
For products that are at all unstable (think reverse tapered wine bottles) or delicate (vaccine vials), the last thing you want is them knocking against each other. Collisions can cause breakage, which often means not only product loss but also that you have to stop the line to clean up broken glass.
Non-glass products can also be damaged. Contact between products can damage labels and screen-printed containers, and any tapered products, especially ones with lips (like yogurt cups), can start to overlap, or shingle. On many accumulation systems, the only way to avoid these outcomes is to slow down the entire line.
You shouldn’t have to slow down your line to accommodate your accumulation system. The ultimate goal is to increase throughput so you increase profits. Your accumulation system should support that goal, not work against it.
Collisions and damage occur because of back pressure. At Garvey, we use a patented pressureless loop technology to eliminate back pressure. The result is that products simply ride along with the conveyor — the chain never moves under a stationary product, and there are no conveyor transfer plates, aka dead plates, between conveyors. Thus, the products never have the opportunity to collide.
When running glass bottles, you can actually hear the difference between our accumulation tables and systems that have back pressure — ours are much quieter because the bottles don’t clang against each other.
For a demonstration of how this works, watch the video below, where we put a raw egg onto an accumulation table with 800 reverse tapered wine bottles.
Easy cleanability
In both the food & bev and pharma industries, cleanliness is a top priority. Not only is a high degree of cleaning and sanitation required by law, but any dirt, grime, or dust in the facility can too easily end up in the product, potentially causing a recall.
But even outside these industries, the value of cleanliness can’t be overstated. Dirt and grease can damage your products and, if those products get out to consumers, harm your brand.
That’s why every piece of equipment in your facility needs to be easy to clean.
All of our accumulation systems are designed for extremely easy cleanability. With a limited return chain, legs, and an elevated base structure, there are no hard-to-reach surfaces. The tracks are open so that any dirt or debris falls straight to the floor, and the conveyor chains can simply be lifted up for power washing.
The short video below shows how simple it is to clean one of our Infinity accumulation systems.
High-speed outfeed
Celebrated NCAA basketball player and coach John Wooden famously said, “It’s the little details that are vital. Little things make big things happen.” That’s just as true in a manufacturing plant as it is on a basketball court. Case in point, by adding a slowdown lane to our accumulation systems, we’ve been able to double, and sometimes even triple, line speeds.
How does something so simple have such a dramatic effect?
On a typical accumulation table, where all of the lanes run at the same speed, products approach the outfeed in a nested formation, as illustrated below.
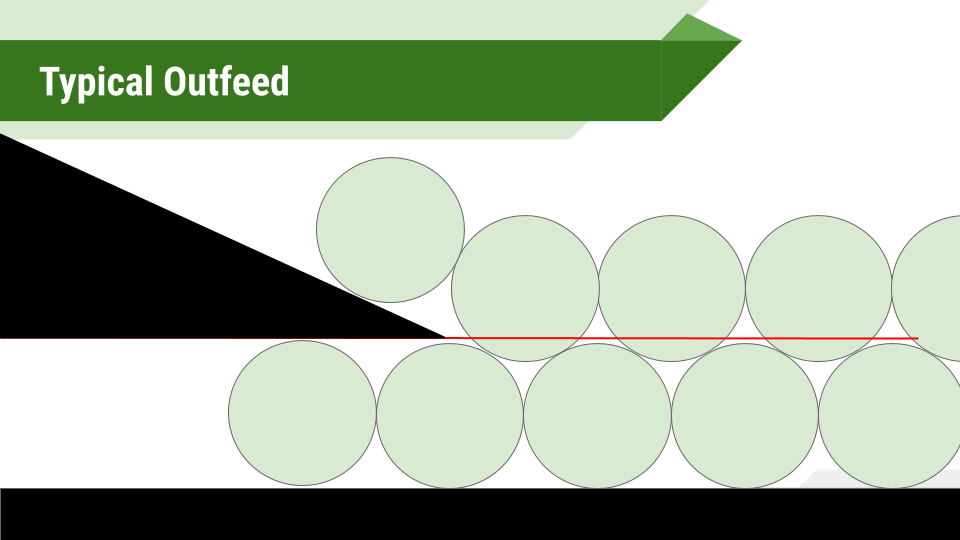
Because of the nesting, the pick off point (i.e., the point where products are redirected to the outfeed lane) hits the nested products where the red line is. The turbulence caused by the impact can create stability issues and damage the product. This is why most accumulation tables can’t run at high speeds — the product instability and damage are simply too great.
To prevent turbulence and the resulting damage, we use a slowdown lane adjacent to the outfeed lane. In the image below, the slowdown lane (in red) is moving 10-15% slower than the rest of the belt.
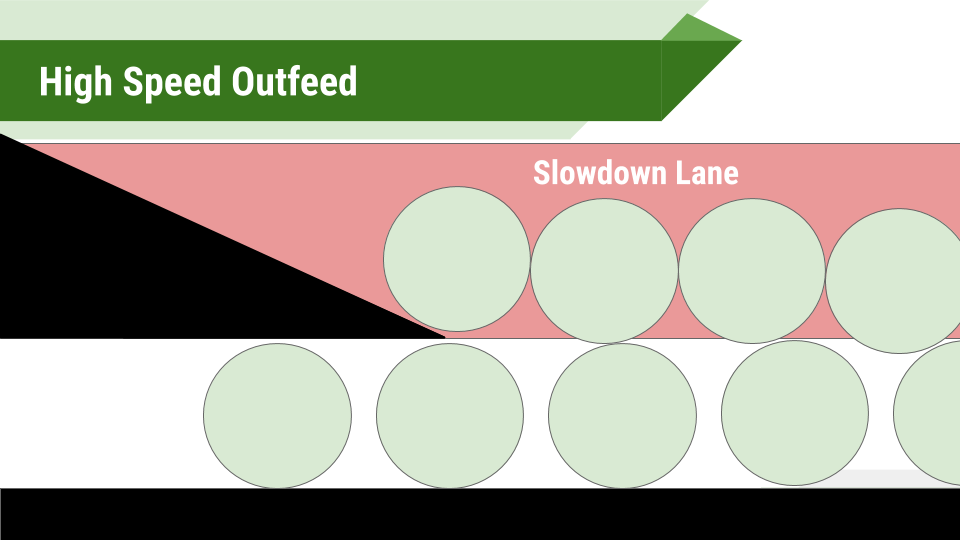
As you can see, when products hit the slowdown lane, rather than nesting between the products in the outfeed lane, they become stacked. This makes them easier to separate without turbulence, solving the stability problem and allowing us to increase the line speed.
On pharmaceutical manufacturing lines, where the stability of small vials is a significant concern, this patented technology allows us to achieve run rates of up to 900 units/minute — the highest rate for single-filing in the industry.
In this video, you can see the difference in the amount of turbulence between running small vials with and without a slowdown lane.
Since we built our first modular conveyor in 1967, we’ve been innovating to provide our customers with the best solutions available. Contact us if you have a project you’d like to discuss.