Food Grade Conveyors for Food Processing & Packaging
Accumulation Tables | Conveyors
Benefits of Garvey equipment
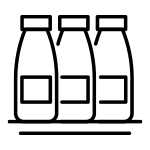
Increase throughput by up to 30%
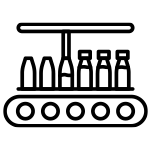
Maximize line uptime by keeping your constraint running
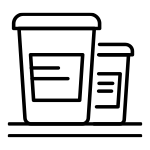
Eliminate product and label damage with patented zero backpressure technology
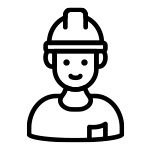
Minimize maintenance costs
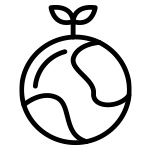
Shrink equipment footprint
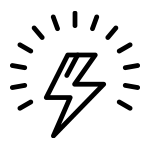
Meet sustainability initiatives with lower energy use
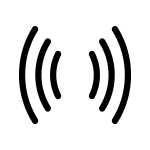
Reduce noise
Food Grade Conveyors: Technical Specifications and Implementation Guide for Accumulation Table Systems

Bagels

Bottled milk

Brownies

Dips

Frozen food trays

Frozen pizzas

Frozen sausage patties

Fruit cups

Granola bars

Pudding

Ready meals

Salad dressings

Sauces

Single-serve jelly

Snack pies and cakes

Yogurt cups
Technical Specifications and Design Considerations
Material Specifications and Compliance

Bagels

Brownies

Frozen food trays

Frozen sausage patties

Granola bars

Ready meals

Sauces

Snack pies and cakes

Bottled milk

Dips

Frozen pizzas

Fruit cups

Pudding

Salad dressings

Single-serve jelly

Yogurt cups
Performance Characteristics and Operating Parameters
Integration and Control Systems
Maintenance and Sanitation Requirements of Food Grade Conveyors
Safety and Compliance Considerations
Cost Analysis and Operational Efficiency
Operational costs include:
Energy consumption, typically ranging from 0.5 to 2.0 kWh per hour of operation
Maintenance expenses, averaging 2-5% of initial equipment cost annually
Cleaning and sanitization costs, including labor and consumables
Replacement component inventory requirements
Installation and Implementation Guidelines
- 480V three-phase electrical service
- Compressed air supply (80-100 PSI)
- Hot and cold water connections for cleaning systems
- Proper drainage systems for washdown procedures
Food Grade Conveyor Quality Control and Validation
Future Considerations and Scalability
System Performance Optimization
Environmental Controls and Monitoring
Advanced Control System Architecture
Sanitary Design Elements
Maintenance Management Systems
Documentation and Training Requirements
Quality Assurance Protocols
Cost Management Strategies
System Validation and Verification
Regulatory Compliance Documentation
Future Tech Integration for Food Grade Conveyor Systems
Risk Management and Mitigation
Advanced Cleaning and Sanitization Protocols
Chemical compatibility represents a critical consideration in cleaning protocols. The food grade conveyor system must withstand regular exposure to cleaning agents including alkaline cleaners, acid-based sanitizers, and quaternary ammonium compounds. The cleaning process typically follows a five-step sequence:
- Pre-rinse
- Detergent application
- Post-rinse
- Sanitization
- Final rinse
Each step requires specific temperature ranges and contact times to ensure optimal effectiveness while protecting system components.
Preventive Maintenance Strategies
Bearing maintenance represents a critical aspect of system reliability. Food grade conveyor bearings require special consideration due to their exposure to both wet environments and cleaning chemicals. The maintenance program includes regular monitoring of bearing temperatures, vibration characteristics, and lubrication conditions. Lubrication procedures must utilize NSF H1 certified lubricants, with careful attention to preventing over-lubrication that could contaminate food products.
Advanced Control System Integration
- Zone loading patterns and utilization rates
- Motor current draw and efficiency metrics
- Temperature variations across critical components
- Cleaning cycle effectiveness through sanitization verification
- Product flow rates and accumulation patterns
Energy Efficiency Optimization
System Redundancy and Reliability
Quality Control and Verification Systems
- Product spacing accuracy and consistency
- Belt tracking and alignment parameters
- Drive system performance metrics
- Cleaning effectiveness through ATP testing
- Temperature control in critical areas
Cost Analysis and ROI Considerations
- Installation costs including utility connections and system integration
- Operating costs including energy consumption and labor requirements
- Maintenance costs including planned maintenance and replacement parts
- Cleaning and sanitization costs including chemical consumption
- Training costs for operators and maintenance personnel
System Documentation and Record Keeping
- Detailed operating procedures for all normal and special conditions
- Maintenance procedures and schedules
- Cleaning and sanitization protocols
- Training materials and competency requirements
- Quality control procedures and verification records
- Compliance documentation and audit records
Advanced Material Handling Solutions
System Components and Accessories
The implementation of proper tensioner systems ensures optimal belt performance while minimizing wear. Conveyor pulleys require precise specification based on load requirements and operating conditions. The integration of cleated belting provides enhanced product control on incline sections, with baffles adding additional flow control capabilities.
Cleaning and Maintenance Solutions
Custom Solutions and Applications of Food Grade Conveyors
System Design and Integration
Performance Optimization
- The specification of proper roller diameter and spacing ensures optimal product support and transfer characteristics.
- Implementation of appropriate cleaning scrapers maintains belt cleanliness while minimizing product contamination risks.
- Integration of tensioner systems ensures consistent belt tracking and operation.
Cost Considerations and ROI Analysis
- Initial equipment cost varies significantly based on system complexity and material selection.
- Installation costs of food grade conveyors depend on system configuration and integration requirements.
- Ongoing maintenance costs include replacement parts and scheduled service requirements.
Technical Support and Service
- Availability of replacement parts ensures minimal downtime during maintenance operations.
- Access to specialized lubricants and cleaners maintains optimal system performance.
- Technical support resources address ongoing operational and maintenance requirements.
Supply Chain Integration and Distribution
Temperature Control and Environmental Considerations
Advanced Material Transport Solutions
- The implementation of joint conveyor sections facilitates smooth product transfer between processing stages.
- Portable food grade conveyor systems provide operational flexibility while maintaining sanitary requirements.
- The integration of powered sections ensures controlled product movement throughout the processing line.
System Configuration and Controls
Maintenance and Cleaning Protocols
- Proper lubrication using food-grade oils ensures reliable operation while maintaining safety compliance.
- The implementation of systematic cleaning protocols prevents product contamination while extending system life.
- Regular inspection and replacement of conveyor parts maintains optimal system performance.
Material Selection and Compatibility
- Stainless steel components provide durability and corrosion resistance in wet environments.
- Urethane belting offers excellent wear characteristics while maintaining food safety compliance.
- The implementation of proper material cleaning procedures ensures ongoing system hygiene.
System Design and Integration
Performance Optimization Strategies
- The specification of proper roller diameter and spacing ensures optimal product support and transfer characteristics.
- Implementation of appropriate cleaning scrapers maintains belt cleanliness while minimizing contamination risks.
- Integration of tensioner systems ensures consistent belt tracking and operation.
Regional Support and Service Networks
- Local service providers ensure rapid response to maintenance requirements across different geographical areas.
- Regional distribution networks maintain parts availability while minimizing downtime during repairs.
- Technical support resources address ongoing operational and maintenance requirements.
Advanced Automation and Control Systems
Material Flow Optimization
Custom Engineering Solutions
- The implementation of custom baffles helps control product flow in specific applications while maintaining sanitary requirements.
- When designing waterfall cleaning systems, careful attention ensures effective belt cleaning while minimizing water consumption.
- The integration of metal detection systems requires precise positioning to maintain inspection effectiveness without compromising product flow.
Systematic Maintenance Approaches
- Wire mesh belting requires regular inspection for damage or wear
- Roller conveyor sections need periodic bearing assessment and lubrication
- Chain driven systems demand careful attention to tension adjustment and wear patterns
- PVC and urethane belting requires regular cleaning and sanitization verification
Regional Compliance and Standards
Advanced Material Selection
- The implementation of hygienic design principles influences material selection throughout the system.
- Engineers must consider factors such as chemical resistance, wear characteristics, and cleaning requirements when specifying system components.
- The integration of proper tensioner systems helps maintain optimal belt tracking while preventing premature wear.
Cost Analysis and Optimization
Manufacturer Selection and System Integration
Used Equipment Considerations
- The condition of motorized components requires thorough inspection, particularly in systems previously used for high-volume production.
- Proper documentation of maintenance history, including lubricant types and cleaning protocols, proves essential for used equipment evaluation.
- Facilities considering pre-owned systems should conduct comprehensive assessments of critical components, including rollers and drive systems.
Regional Support Networks
Maintenance and Lubrication Requirements
Cleaning System Integration
Temperature Management
Component Selection and Integration
Advanced Control Systems
Training and Certification Requirements
Troubleshooting Guidelines
Lifecycle Management
- Regular cleaning and sanitization impact on wear rates
- Operational demands on critical components
- Environmental conditions affecting system longevity
- Availability of replacement parts from suppliers near facility locations
Industry-Specific Applications
Comparative Analysis
- Operational costs including oil and lubricant consumption
- Maintenance requirements and local support availability
- System reliability and production impact
- Integration capabilities with existing equipment
- Regional support infrastructure from Delhi to Kentucky
Future Technology Trends
- Enhanced integration with Industry 4.0 principles
- Advanced grad(e) monitoring and control systems
- Improved energy efficiency in motorized systems
- Enhanced cleaning and sanitization capabilities
- Sophisticated diagnostic and maintenance prediction systems